



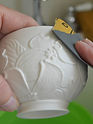

One of a Kind Porcelain-
My one of a kind pieces begin with Grolleg Porcelain on the potters wheel. The pots are allowed to partially dry to a “leatherhard” state. Working from live specimens and resource photos, I use watercolor paints to sketch the botanical images onto the pot surface. This allows me to make changes and the paints burn away during the firing. Then, using an assortment of tools including exacto knives and dental tools, I begin carving away the background clay to reveal the raised bas-relief botanical images. Small amounts of clay are sometimes added to the surface. The carving process often takes as much as one hundred hours for one pot. When dry, the pot undergoes the first firing to 1800F, after which it is sanded and polished. The second firing is to 2200F. I further enhance the unglazed porcelain surface by hand polishing each piece after the final firing. Each One of a Kind piece is finished with gold leaf on the bottom.
Limited Edition Porcelain-
My Limited Edition Porcelain pieces begin in exactly the same manner as my One of a Kind pots. They are wheel thrown, sketched, carved, dried, fired and sanded and polished. After they have been fired the first time, a multi-piece plaster mold is made of the pot. Liquid porcelain called slip is poured into the mold. The slip that adheres to the plaster mold becomes the pot when the excess slip is poured out. When this “cast” pot is released from the mold it requires extensive clean up and refinement. Beyond the obvious cleaning of mold seams, I also re-carve much of the bas-relief surface. I carve back all the fine details and undercuts that are lost in the casting process. It is this attention to detail that I believe brings back the life and spirit of the original carving. The edition, the number of the casting ( 1/100) can be found on the bottom of the pot.